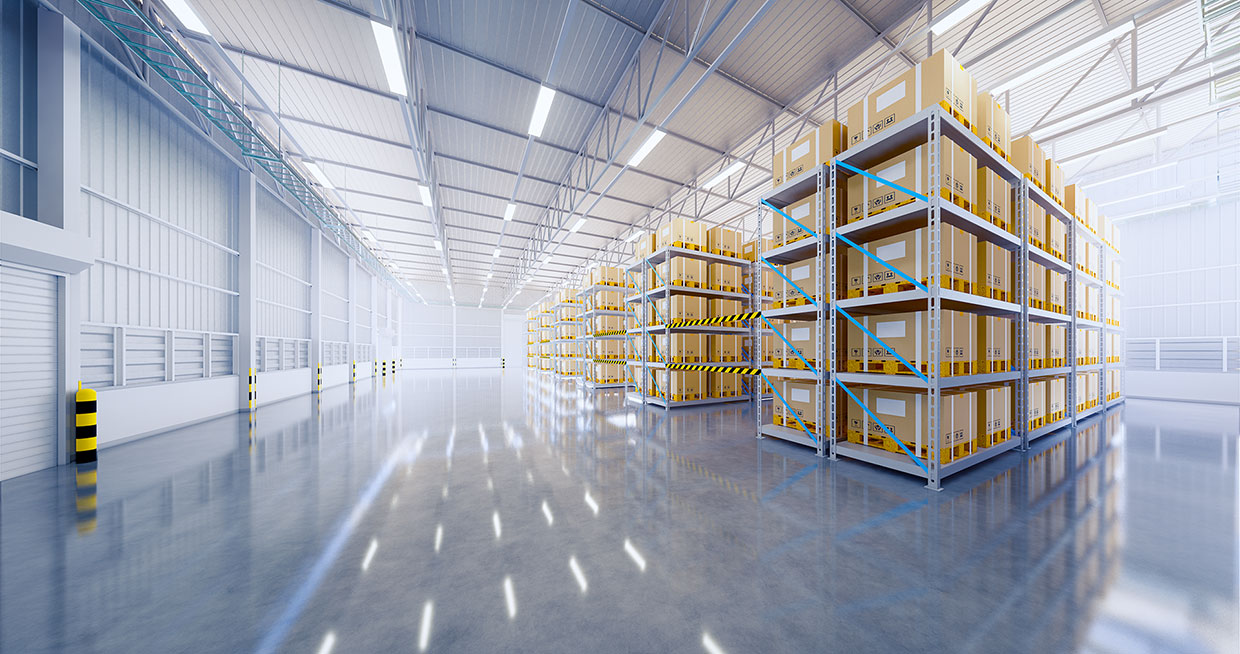
Artificial Intelligence (AI) has been one of the great buzzwords of the last decade, alongside Big Data, machine learning, and digital transformation. For those who do not work in tech, these are concepts difficult to envisage in the form of real-life applications. However, the last few years have seen concepts start to leap from the page and become tangible solutions with roles to play in our homes and workplaces. One industry making impressive headway in this field is the warehouse industry which is fast becoming a showcase of what artificial intelligence solutions look like, the roles they fulfill, and the quantifiable benefits they bring to the bottom line.
In this blog post, we look at a handful of artificial intelligence solutions and explore how they are improving warehouse operations and management.
Firstly, what do we mean by Artificial Intelligence?
Artificial Intelligence, as we talk about in this blog, is the term used to describe a machine or system able to perform actions based on information it receives digitally. Technologies like cloud computing and Hadoop are empowering Big Data and enabling companies to store extraordinarily vast amounts of data including text, audio, and images. Complementary technologies have been developed to capture more data (e.g. sensors) and exploit the data, (e.g. machine learning, which works by giving a computer a goal, some instructions (algorithms), and a huge data set with which to teach itself how to achieve its goal, for example, recognize a human face).
Let’s take a look at some real-life applications of artificial intelligence in the warehouse industry.
Robotics
Robots are the classic face we put to AI, and in the case of warehouse operations, this is now a reality that is bringing huge efficiency and productivity gains in the picking process.
Picking is a fragmented process prone to human errors such as picking the wrong product, incorrectly placing it on the picking wall, or attaching the wrong address. With low margins in warehouse management, such errors quickly erode profit.
In 2018, DHL introduced LocusBots™ into their warehouse operations. The robots, which are essentially self-driving carts with a computer screen displaying key information, guide pickers to the correct location, product, and deposit basket, while alerting the picker to any mistakes made during the process. The bots use “machine vision” to navigate around the warehouse, and are fed information from other systems that enables them to automatically prioritize next-day deliveries. DHL reported that bots had led to an increase in picking productivity from 70-80 units per day when using cart pulling to 150-180 units daily, and a reduction in order fulfillment time from 5 to 1-2 days.
Augmented Reality
E-commerce is constantly adapting to trends and triggering new ways of doing business which means warehouse managers need to adapt fast – especially 3PL warehouse managers. Warehouse layout is fundamental to having efficient warehouse operations, so when it needs to change, it has to be right.
Augmented reality brings tremendous benefit to this scenario. Augmented reality glasses enable warehouse planners to walk the floor while visualizing in 3D what the proposed layout changes would look like, and simultaneously test whether they would work. This ability to simulate changes, rather than having to implement then trial them, brings huge time and cost savings, and makes operations more flexible to change in the long run.
Voice Recognition
Voice Recognition is another AI application enhancing picking. In this case, Natural Language Processing is used to convert text information related to the order, such as product number, into audio. This audio is delivered to a headset worn by the picker. Once a picker has located the correct product, they confirm, also via voice, that the instructions have been completed.
Warehouses are adopting voice recognition technology in order to make picking both more efficient and safer. Without the need to hold a scanner or hit buttons, pickers can work hands-free, and fewer visual checks against numbers or other information reduce eye strain.
Internet of Things
The Internet of Things generally refers to the use of sensors to collect data and automatically feed it into other data processing and decision-making systems.
A successful case study of sensor deployment has been by cold storage facility Lineage Logistics who were looking for a way to reduce their energy consumption and costs. One obvious solution was to pull more energy from the grid at night when electricity was much cheaper compared to during the day. Sensors enabled them to implement this strategy which saw them overcool their facilities at night and then automatically manage the temperature inside the warehouse through the use of over 1,000 sensors and artificial intelligence software that triggered the freezers to power up only when needed.
In 2018, they calculated the impact to be $4 million in savings and 34% reduction in energy consumption.
While the majority of warehouses are still in the early stages of their own digital transformation, these examples show that AI will soon be a staple of warehouse operations.